- The CHISAKI LIME KILN Burns All Kinds of Lime.
@The specialty of the CHISAKI LIME KILN can burn 10 to 35mm high density limestone and crystalline limestone, and also the coral reef and shell, which is very difficult to burn by the existing kilns.
- The High Efficiency Heat Consumption and Stable Operation
@The perfect burning condition is accomplished by setting only one burner
in center, and by moving limestone with the pusher rods action on the rotating
hearth.
@As the result, the re-burning process will
not be necessary because of no soot in bag filter other than the dust.
- The Best Suited 200 ton/day Production
@The most efficient design size of the
CHISAKI LIME KILN is 100 ton/day.
@Customers provide 2 sets of them to
accomplish the most efficient and stable productivity.
- The Highest Quality Lime Production
@The high level calcination is accomplished by precise control of the ejector
air, and produces the highest quality lime, which is used for the production
of the high quality steel, and the precipitated calcium carbonate as well.
- The lowest Cost of The Operation and maintenance
@The compact and simple design of the CHISAKI LIME KILN can stand for the
lowest heat consumption and maintenance cost, minimized man power of operation
and easy response to any troubles to happen.
|
|
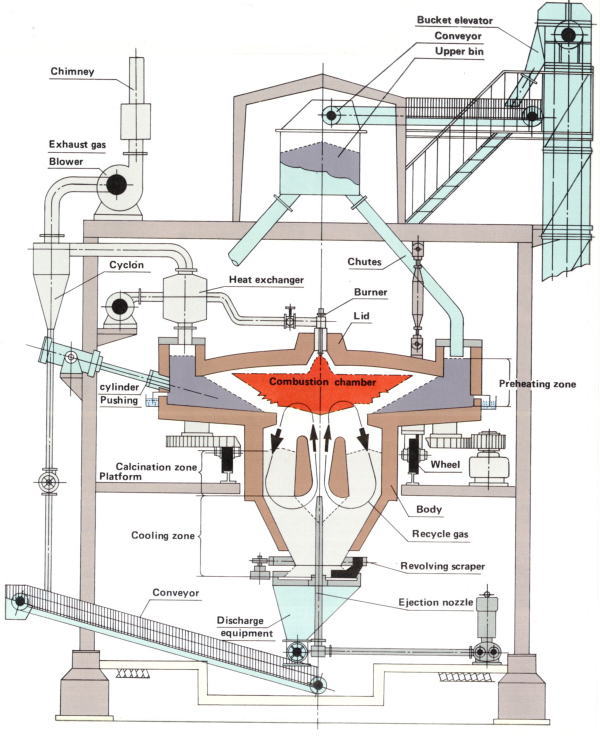 |
|
Limestone of size 10 - 35 mm is fed into the upper bin, from which several
chutes distribute limestone onto the preheating zone.
Main body of the kiln as well as the flat hearth rotate intermittently, contributing to transfer solids along the perimeter of the hearth, and then enabling the uniform feeding of solids from every chute onto the bed of the preheating zone.See Figure 2.
|
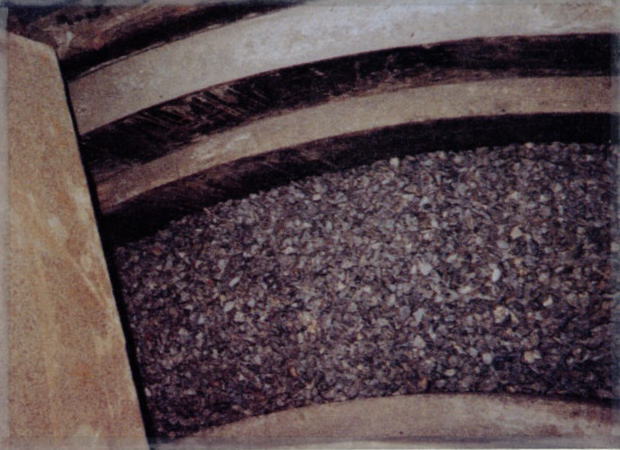 |
|
@Figure 2. Uniform Feeding of Solid on The Upper Surface of The Preheating
Zone |
Usually 6 to 10 sets of cylindrical pushers are positioned around the preheating
zone, which push down solids at the bottom of the preheating zone as seen
in Figure 3. Note that solids surrounding a pusher are also pushed down. |
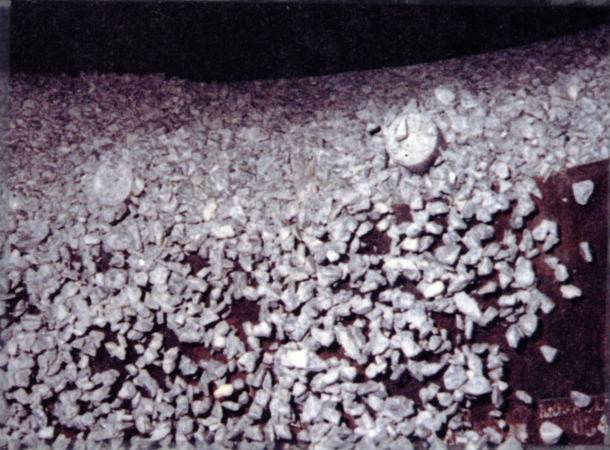 |
|
Figure 3. Solids Are Pushed Down by Cylindrical Pushers |
Movement of solids caused by the action of
the rotating hearth combined with the cylindrical pushers makes the flow
pattern of solids to be quite uniform. Because of this, exact and low height of the
preheating zone is established, making sure the uniform flow pattern of gas
stream within it, and resulting in the low pressure drop in spite of small
size.
Peripheral movement of solids on the hearth
enables the uniform contact of solids with combustion gas stream, and then
nearly the ideal heat exchange is carried out between solids and the combustion
gas streams.
In short, rotation of the hearth assures
the efficient contact between combustion gas and solids streams in the
preheating zone.
|
|
|
As seen in Figure 3, cylindrical pusher
extrudes down the solids surrounding it, thus feeding them uniformly onto the
lower portion of the kiln. Power consumption of the pusher is small,
because of its small contacting surface with the bed of solids.
More than 50% of calcination reaction takes
place at the bottom of the preheating zone, where temperature of solids is
close to 900. Furthermore, the mean temperature of the combustion
chamber is as high as 1200, and then the
radiant heat transfer to the edge of the pusher is very intense, which gseesh
the combustion chamber intermittently. See
Figure 3. In
spite of such severe circumstance with temperature, trouble free operation of
the cylindrical pushers has been confirmed through practical operations longer
than 20 years. It
should be noted that special cooling system is unnecessary for the pusher.
|
|
- Burner Easy to Control, Pollution Free Combustion
|
Only one or at most two burners are positioned downwards nearly at the
center of the circular lid of the kiln. Burning of fuel in the combustion
chamber is easy to control through visual or other instrumental measurements.
One can use any type of fuel; for instance, fuel gas, kerosene, crude oil,
heavy oil, pulverized coal or other combustible materials.
As seen in Figure 1, combustion is carried out in a wide combustion chamber,
accompanied by the violent mixing with the air stream, realizing nearly
complete combustion. Fuel gas from this type of kiln is thus quite clean,
and electrostatic precipitator or even bag filter is usually unnecessary
to meet the stringent environmental regulation in Japan.
Flame and combustion gas in the combustion
chamber have enormous ability to emit thermal radiation. Sum of the radiant
heat transfer to the bed surface of limestone at bottom of the preheating zone,
as well as to the upper bed surface of the solids in the main body of the kiln,
corresponds to nearly one half of the theoretical energy required for calcination
reaction.
|
|
- Ejector Assures Uniform Calcination
|
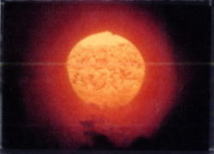 |
Nearly half of calcination reaction takes place in the lower bed of the
kiln. Again, rotation of the main body transfers solids peripherally, resulting
in good contact between solids and combustion gas streams.In addition,
uniform distribution of solids is attained on the surface of the bed due
to the rotation of the hearth. Figure 4 shows the visual observation at
the surface of the bed in the main body of the kiln.
|
Figure 4. Visual Observation at The Surface of Calcination Zone |
|
|
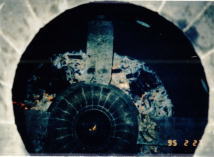 |
In order to calcine solids thoroughly, an ejector is positioned upward
along the center line of the kiln. See Figures 1 and 5.
The air is ejected from a nozzle into the diffuser, shown in Figure 5,
and induces combustion gas from the lower surface of the bed as seen in
Figure 1.As the result, considerable amount of combustion gas circulates
downward through the bed of solids. By means of this circulation, very
uniform and nearly complete soft calcination is carried out in the bed,
and then quality fluctuation in the product is eliminated. |
Figure 5. Diffuser for The Ejector |
|
|
Because of the reason above mentioned, heat
exchange between solids and air streams in the cooling zone of the lower bed is
nearly ideal, giving temperature of discharged product to be only 60. And
because of some part of solids in the cooling zone are cooled off by the heat
exchangers which are provided for preheating of ejector air, the volume of the
air through cooling zone is reduced. Thus
water content of the quicklime is lower than the one processed in the
conventional shaft kiln. |
|
|
Since solids of small size can be
processed, necessary residence time of solids in the kiln is far less than in
any conventional shaft kilns.
Because of product solids are quickly discharged from the bottom of the
CHISAKI LIME KILN, response to the variation of operating conditions can
be quickly detected.Therefore, it will be easy to set the high level of
operating condition for the required gQuality Controlh.Advantages by low
ratio of the kiln diameter (D) and height (H), (H/D) is less than 1.5.
1. The low center of gravity because of low height of the equipment, gives
lighter support structure and compact foundation.
2. Raw materials of weak mechanical strength such as coral reef and shell
can be calcined because of low bed height of kiln.
3. Extremely low dust generation in the kiln, only 2 - 3 kg/CaO.ton
4. Easy to install equipment above the kiln, for example solve following
problems by installing large raw material storage bin.
a. Shortage of storage area in the factory
b. Carry-up operation of raw material only at day time because of noise
regulation at night
c. Protection of raw material freezing
|
|
- Capacity and Heat Consumption
|
The CHISAKI LIME KILN is designed to process solids of small size, and
nearly the ideal heat exchange is achieved between solids and gas streams,
making its capacity per unit volume is quite large.In other words, the
CHISAKI LIME KILN of given volume can calcine far larger amount of limestone
compared with the other types of same volume.
Substantially, counter-current heat exchange is carried out with moving
bed contacting principle, resulting in high thermal efficiency even for
such production of lime as small as 50 - 100 ton/day.With respect to any
types of kilns, usually they say that the larger unit we use, the higher
efficiency we get.The CHISAKI LIME KILN challenges to overcome this industrial
tradition.
|
|
- High Technology Requires A Number of Small Kilns
|
Along with the recent development of new
inorganic substances in advanced technologies, requirement to the quality of
calcined lime is getting to be stringent, giving different severe
specifications for different purposes.
Conventional large lime kilns cannot satisfy above requirement, because
special operation should be made to meet such severe specification, which
differs from purpose to purpose. It is predicted that a number of small
kilns may replace conventional large lime kilns, in parallel to the development
of new inorganic substances with high quality and special functions. The
CHISAKI LIME KILN can contribute much in producing lime of high quality
with different specifications from purpose to purpose.
|
|
- Reformation of Conventional Kiln
|
In case any conventional shaft kiln becomes old and cannot satisfy the
recent requirement for the quality of its product, it can be reformed to
the CHISAKI LIME KILN easily, with far less construction cost than constructing
new kiln of any conventional type. Foundation support structure, blowers,
housing and other else which belong to the existing kiln can be utilized
in its reformation to minimize the construction cost.
Several old shaft kilns have had this reformation, and their performance is as good as the CHISAKI LIME KILN of ordinary design. Top half of the old kiln is utilized as the bin of limestone, having bottom half replaced the rotating the CHISAKI LIME KILN, which produces lime of far higher quality than the old one with higher efficiency.
|